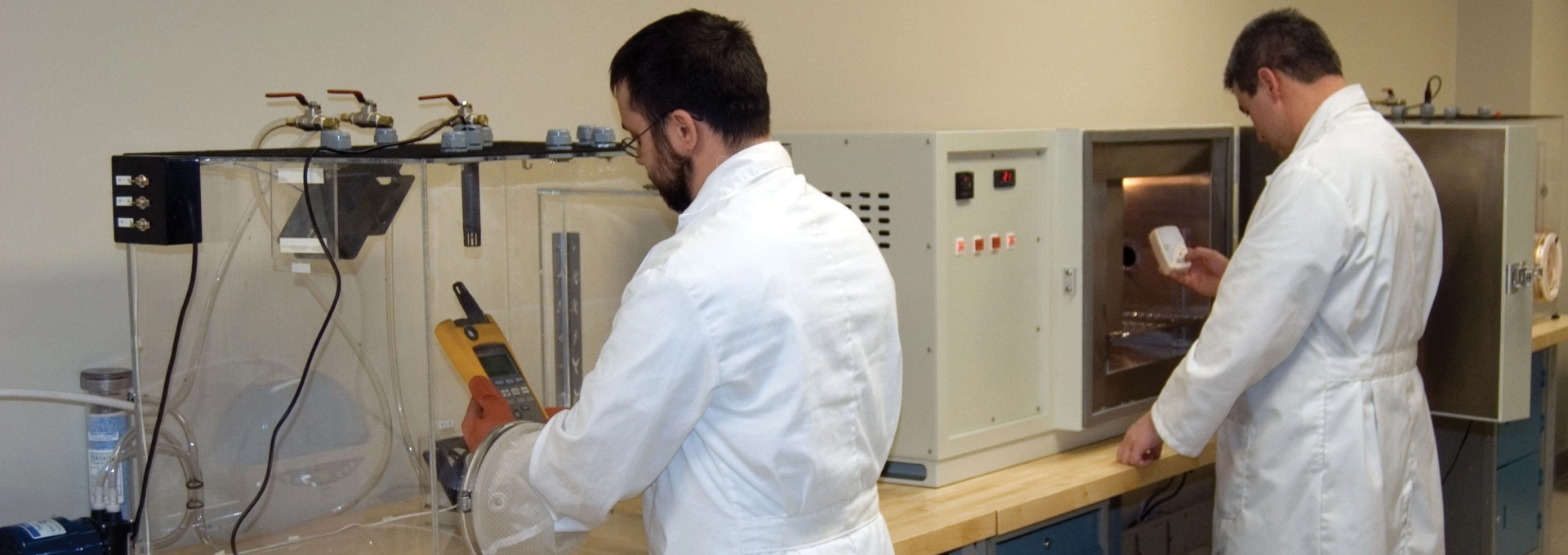
Semiconductor manufacturing equipment represents a significant investment for any production facility, with individual machines often costing millions of dollars. The complexity and precision required in semiconductor fabrication make proper maintenance and repair crucial for maintaining production quality and efficiency. Professional repair services have become essential as semiconductor equipment grows increasingly sophisticated, requiring specialized knowledge and tools for proper maintenance and troubleshooting.
Expertise ensures proper diagnosis repair procedures
When dealing with complex semiconductor equipment, accurate diagnosis is crucial for effective repairs. Professional technicians from a reputable semi-conductor production machine repair company bring years of specialized experience and training to identify issues quickly and accurately. Their expertise allows them to understand the intricate relationships between different system components and how they affect overall equipment performance.
These professionals undergo continuous training to stay current with the latest semiconductor manufacturing technologies and repair techniques. Their deep understanding of semiconductor physics and equipment operation enables them to identify both obvious malfunctions and subtle performance degradation that might otherwise go unnoticed.
Professional semiconductor equipment repair technicians typically have 5-10 years of hands-on experience before handling complex repairs independently, ensuring the highest level of expertise for critical equipment maintenance.
Specialized tools equipment guarantee optimal results
Professional repair companies invest heavily in specialized diagnostic and repair equipment that isn’t typically available to in-house maintenance teams. This sophisticated toolset enables technicians to perform precise measurements, calibrations, and repairs that meet manufacturer specifications.
Access to latest diagnostic repair technologies
Modern semiconductor equipment repair relies heavily on advanced diagnostic tools and testing equipment that can detect microscopic issues. Professional repair companies maintain an extensive array of specialized testing devices, including:
- High-precision electrical testing equipment
- Advanced thermal imaging systems
- Specialized alignment tools
- Calibrated measurement devices
Extensive inventory of High-Quality replacement parts
Professional repair companies maintain relationships with original equipment manufacturers (OEMs) and authorized parts suppliers. This ensures access to genuine replacement components that meet exact specifications. Using certified replacement parts is crucial for maintaining equipment warranty and ensuring optimal performance.
Properly calibrated instruments for precise adjustments
The accuracy of semiconductor equipment depends heavily on precise calibration. Professional repair companies maintain their tools and instruments according to strict calibration schedules, ensuring measurements and adjustments meet industry standards. Regular calibration of testing equipment is essential for maintaining measurement accuracy within the tight tolerances required by semiconductor manufacturing.
Rigorous quality control minimizes costly downtime
Professional repair services implement comprehensive quality control procedures throughout the repair process. This systematic approach helps prevent recurring issues and ensures repairs meet manufacturer specifications. Quality control measures typically include:
- Initial equipment assessment and documentation
- Verification of repair procedures against OEM specifications
- Post-repair testing and validation
- Performance monitoring during initial restart
The implementation of these rigorous quality control measures can reduce equipment downtime by up to 40% compared to repairs performed without proper protocols. This translates directly into significant cost savings and improved production efficiency.
Experienced technicians adhere to safety protocols
Working with semiconductor equipment involves handling potentially hazardous materials and high-voltage systems. Professional repair technicians are trained in proper safety procedures and emergency protocols. They understand the importance of maintaining clean room conditions and preventing contamination during repairs.
Safety statistics show that professional repair services have significantly lower incident rates compared to in-house repairs, largely due to comprehensive training and strict adherence to safety protocols.
Safety Aspect | Professional Service | Non-Professional Service |
---|---|---|
Safety Training Hours/Year | 80+ | 20-30 |
Incident Rate (%) | 0.5 | 2.3 |
Safety Protocol Compliance (%) | 98 | 75 |
Comprehensive documentation facilitates regulatory compliance
Professional repair companies maintain detailed records of all maintenance and repair activities. This documentation is crucial for regulatory compliance and equipment certification. Each repair typically generates comprehensive reports including:
The documentation process includes tracking of repair histories, calibration records, and performance data. This information proves invaluable for preventive maintenance planning and regulatory audits. Professional repair companies use specialized CMMS
(Computerized Maintenance Management Systems) to ensure accurate record-keeping and traceability.
These detailed records also help identify patterns in equipment performance and potential areas for improvement. By analyzing repair histories, professional services can recommend preventive maintenance schedules that reduce the likelihood of future failures and extend equipment lifespan.